Im Museum Unteres Schloss finde ich wenig Informationen über die Geschichte zum VEB Greika Greiz1. Ich hatte mir mehr erhofft, zumal auf der Internetseite der Stadt Greiz über die Textilausstellung des Museums folgende Informationen zu finden sind:
“Die ehemaligen Wirtschaftsräume für den fürstlichen Hof beherbergen seit 1998 eine Schauwerkstatt zur Herstellung und Geschichte des Greizer Textilwesens. Die Weberei und später die Textilindustrie mit den textilverarbeitenden Gewerken prägten Greiz über 500 Jahre…“
Meine Verwunderung darüber teile ich einer Mitarbeiterin am Eingang des Museums mit. Sie antwortet, dass es kaum noch Menschen gibt, die über Webstühle, Strickmaschinen usw. Auskunft geben könnten.
15 Minuten später treffe ich mit Herrn H. und Herrn D. auf zwei Greizer mit umfangreichem Wissen über Textilindustrie und deren Geschichte.
Zu Beginn des Gespräches sagt Herr Hildmann, dass sie versuchen werden, mir meine Fragen zu beantworten. Ich bin etwas verlegen. Die einzige Vorbereitung auf das Treffen sind die Informationen, die ich von den Frauen über die Stoffe und Muster erhielt bzw. den Archivunterlagen entnommen habe. Ich frage nach dem Gründeldruck und erhalte knapp zwei Stunden Information an Information.
Cirka 1963 stellte die volkseigene Chemieindustrie massig Polyesterseide zur Verfügung. Da die Seide selbst kein Wasser aufnimmt, wurde das Gewebe auch für Regenschirme eingesetzt, erzählt Herr Dietz, ehemals Haupttechnologe und Färbereileiter. Farbstoffe sind in der Regel im Wasser gelöst. Nur wenn man das Gewebe mit einer Farbstoffwasserlösung zusammenbringt, tritt eine Färbung ein. Da aber Polyester kein Wasser aufnimmt, gab es nur eine Methode mit Hochtemperatur, die so genannte Thermosolfärbung: das Gewebe läuft durch eine Farbstoffwasserlösung, die Farbe wird mit zwei Walzen auf das Gewebe gedrückt und anschließend sofort getrocknet. Im Anschluss läuft es über eine Siebtrommel mit 180-210 Grad heißer Luft. In diesem Bereich wird die Seide plastisch und die Farbe kann eindringen. Jeder Faden der Polyesterseide, erklärt Dietz weiter, weist eine andere Struktur auf. Beim Färben des Gewebes, welches aus Kette und Schuss besteht, kam die Kettstreifigkeit zum Vorschein. Wir als Färber haben es nicht zustande gebracht, dass jeder Faden so gefärbt wird, dass ein einheitlich gefärbtes Gewebe entsteht. Beim schwarzen Herrenschirm hat sich das dann in der Durchsicht bemerkbar gemacht, was auch anschließend reklamiert wurde. Übertrieben gesprochen hat man im Schirm helle (antrazitfarbene) und dunkle Fäden gesehen.
In einem Zeitungsabschnitt der kombinatseigenen Zeitung Solidor Nr.8/1982 aus den Unterlagen von Frau Munzert heißt es:
Ein makelloses Schwarz bereitete übrigens den Schirmmachern lange Zeit das meiste Kopfzerbrechen, denn das durch den aufgespannten Schirm fallende Licht gab den geringsten Farb-, oder Gewebefehler schonungslos preis. Der jetzt angewandte sogenannte Gründeldruck legt die Farbe rasterähnlich auf das Gewebe und garantiert damit einen gleichmäßigen Schwarzeffekt.
Herr Hildmann, ehemals Leiter der Druckereiabteilung, erzählt dass der Begriff Gründeldruck ein ortsspezifischer Fachausdruck aus der Druckerei in Greiz war. Auf dem gefärbten Gewebe wurde zusätzlich mittels einer 1000PunktDruckwalze Farbe aufgedruckt, um einen gleichmäßigen Farbton zu suggerieren. Man erhielt kein 100prozentiges schwarz, auch kein 100prozentiges Marine, eher, so Hildmann, einen geringfügig helleren Druck als ganz dunkel.
Es wurde aber auch bei größeren Mustern direkt auf dem weißen, ungefärbten Stoff gedruckt. Um auch hier die Dispersionsfarbstoffe mit dem Gewebe zu fixieren, arbeitete man mit Hochtemperaturdämpfern, erzählt Hildmann. Dem Wasser wurden verschiedene chemische Mittel zugesetzt, unter anderem Verdickungsmittel wie Algen oder Tang, die den Farbstoff in Form gehalten haben. Die Temperatur beim Dämpfen betrug 130 Grad.
Im Stoffdruck muss man Folgendes sagen: man geht von Dunkel nach Hell und beginnt mit der ersten Walze in Schwarz, Marineblau, Schwarzbraun, Schwarzoliv oder Dunkelpurpur. Damit erzielt man den besten Kontrast, so Hildmann. Die Muster waren auf den Walzen graviert und stammten aus dem Walzengravierwerk in Frankenberg/Sachsen. Die Oberfläche der eingefärbten Walzen wurde durch einen Rakel von der überschüssigen Farbe befreit. Die vertieft liegende Mustergravur übertrug die Farbe auf das Gewebe.
Je nach Größe der Muster mussten die Drucker Rakelblätter (Abstreichmesser) in verschiedenen Stärken verwenden. Hildmann erzählt, dass es eine große Handwerkskunst war, diese scharf anzuschleifen. Es gab aber auch Schwierigkeiten. Bei einem großen Muster ist das Messer mitunter auf einfünftel eingefallen und wenn viel gedruckt wurde, mussten neue Walzen in Frankenberg bestellt werden. Das war mit viel Aufwand und viel Geld verbunden, denn das Muster wurde dazu wieder ausgelegt, die Walze musste bestellt, geholt und in die Maschine eingebaut werden. Hinzu kamen natürlich verbindliche Liefertermine. Ein Dessin, so Hildmann, wurde in vier verschiedenen Farbstellungen (Colorits) hergestellt. So konnte die Schirmfabrik ihren Kunden verschiedene Schirme anbieten.
Herr Dietz fasst den Ablauf des Gewebes von der Appretur2 bis zur Nachbehandlung noch mal zusammen. Nachdem der Stoff gefärbt und /oder bedruckt wurde, wurde er anschließend über Breitwaschmaschinen gereinigt, um den nichtgebundenen Farbstoff abzuwaschen. Das Gewebe wurde getrocknet und anschließend mit einem Hydrophobierungsmittel oberflächlich behandelt. Anfänglich gab es häufige Reklamationen seitens der Schirmfabrik, dass der Hydrophobierungseffekt zu gering war. Das Gewebe ging daraufhin durch eine Kalander-Maschine. Eine der beiden Walzen hatte eine Temperatur von 200Grad und so konnte das Hydrophobierungsmittel in die aufgeweichte Faser eindringen und die Zwischenräume, die für den Durchsprüheffekt verantwortlich waren, wurden dabei etwas mit verquetscht.
Dietzes Frau arbeitete im Labor, wo jede Charge auf den Durchsprüheffekt hin kontrolliert wurde, bevor diese dann mit Zertifikat der Schirmfabrik übergeben wurde. Restlos zubekommen hat man die Zwischenräume nie, so Dietz, das war eben der Nachteil der Polyesterseide. Herr Hildmann hebt aber die Festigkeit und Hochwertigkeit dieses Gewebes hervor.
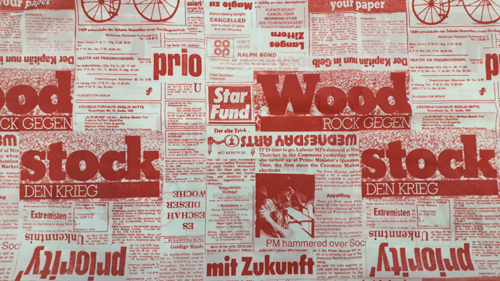
Während des Gespräches öffnet Hildmann einen Koffer und zeigt mir eigene Schirme und Stoffreste. Einer erinnert an einen Zeitungsdruck. Er schenkt ihn mir und sagt dazu, dass dieses Muster von der gesamten politischen Elite der Greika und der Schirmfabrik wegen der englischen Begriffe begutachtet wurde. Gemeinsam mit Dolmetschern wurde er abgesegnet. In Marine sind die fertigen Schirme besonders gut gelaufen, erinnert sich Hildmann. Ich erkundige mich nach Gestaltern der Muster und erfahre, dass es im Betrieb ein Musterbüro gab, in dem 15 Personen arbeiteten. Viele haben in Schneeberg, in Halle an der Burg Giebichenstein oder Berlin Weißensee studiert. Leider gibt es kaum noch Kontakt.
Einen Tag nach dem Treffen erinnere ich mich an die Ausstellung und das Gespräch. Ich empfand Traurigkeit darüber, dass es so viele Menschen gibt, die ihr Wissen nicht weitergeben werden, weil keiner danach fragt und Unverständnis über das Hofieren der Fürstenfamilie Reuß im Museum. In welchem Verhältnis steht ihre Geschichte zur Geschichte der Greizer Menschen? Wieviele von ihnen waren bis zur Wende in der Textilindustrie beschäftigt?
1 Das Akronym Greika entstand 1953 aus der zuvor üblichen Bezeichnung des VEB Greizer Kammgarn-Weberei (https://de.wikipedia.org/wiki/Greika)
2 Appretur (von frz. apprêt „Ausrüstung, Zurichtung“) bezeichnet die veredelnde Behandlung von Stoffen und Textilien, aber auch Garnen und Fasern sowie Papier und Leder, um ihnen ein besonderes Aussehen und/oder bestimmte Eigenschaften zu geben. (https://de.wikipedia.org/wiki/Appretur)